5 mln komponentów rocznie. Polska fabryka najważniejsza w koncernie
Często usłyszeć można, że rola ulokowanych w Polsce fabryk motoryzacyjnych sprowadza się w istocie do końcowego montażu gotowych elementów i jako kraj stanowimy jedynie rezerwuar taniej siły roboczej. To krzywdzący stereotyp. W Polsce zaleźć można wiele wiodących zakładów produkcyjnych z branży automotive, które nie tylko wyznaczają kurs jakim podążają fabryki na całym świecie, ale też dysponują własnymi działami badań i rozwoju.
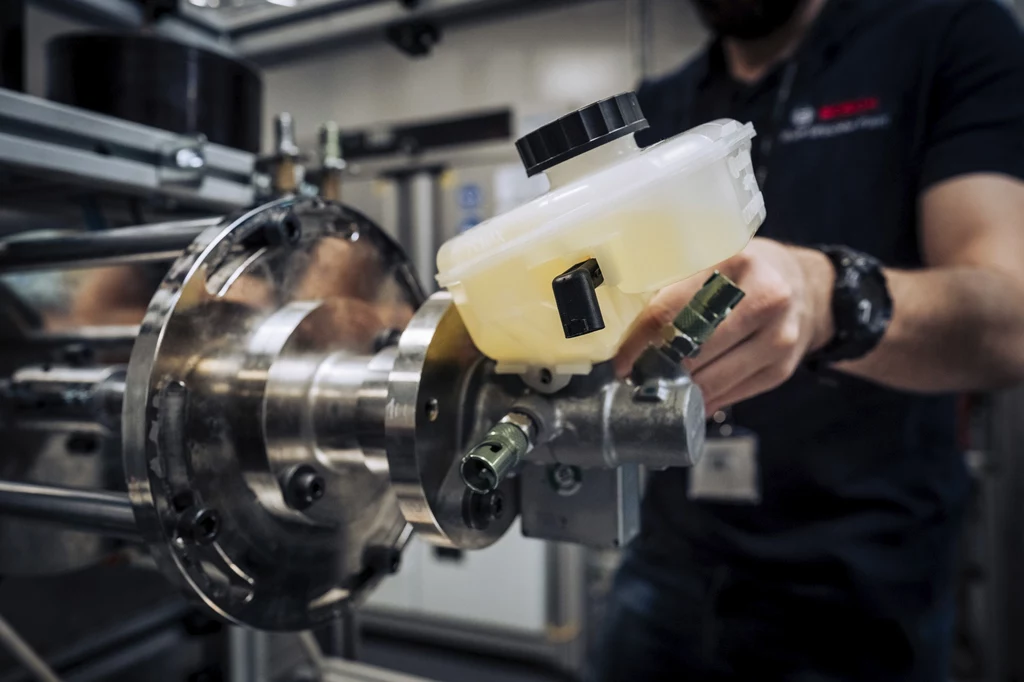
Spis treści:
Świetnym przykładem jest chociażby zakład firmy Bosch w podwrocławskim Mirkowie, gdzie powstają serwa i pompy hamulcowe dla zdecydowanej większości produkowanych obecnie w Europie pojazdów. Warto dodać, że przynajmniej połowa z nich ma pod maską części, za opracowanie których odpowiadali polscy inżynierowie.
Fabryka przyszłości działa pod Wrocławiem. Jedno serwo co 3 sekundy
W fabryce Boscha pod Wrocławiem, której historia w obecnej lokalizacji sięga 2003 roku, produkowane są dziś elementy układu hamulcowego. Ściślej - chodzi o tzw. zespoły mocy, czyli serwa hamulcowe (wraz z pompami hamulcowymi) oraz czujniki prędkości obrotowych kół. Statystycznie - jeden zespół mocny powstaje tu co 3 sekundy. Co 1,5 sekundy z linii zjeżdża też nowy czujnik wykorzystywany chociażby w układach ABS czy ESP.
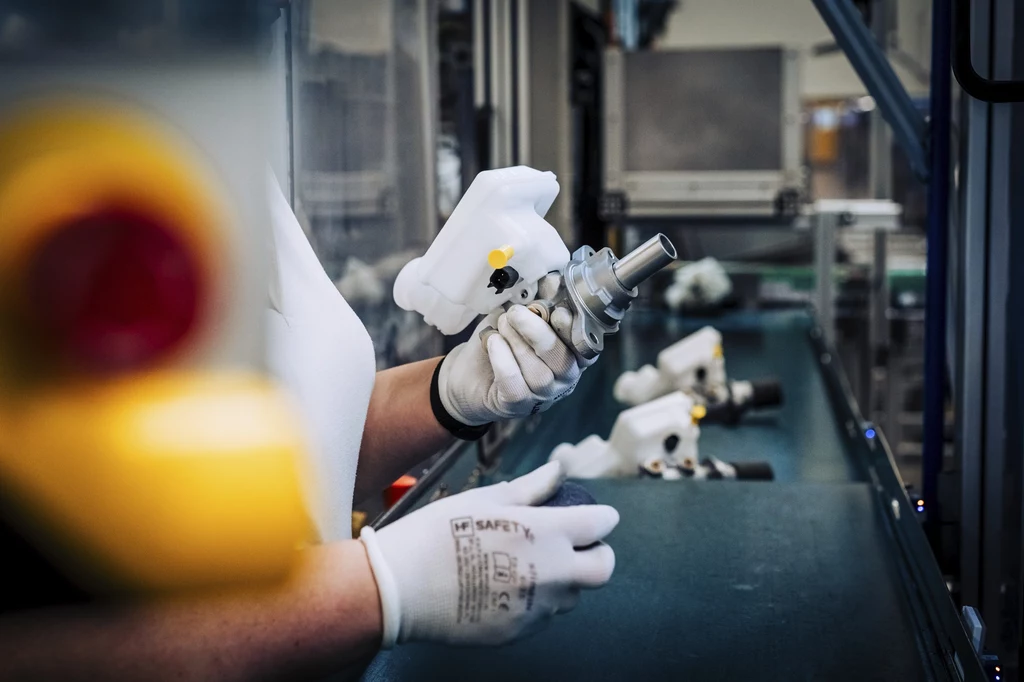
Dolnośląski Mirków jest ważnym miejscem na mapie fabryk Boscha. To "wiodąca lokalizacja" (ang. lead plant) międzynarodowej sieci produkcyjnej układów hamulcowych Bosch złożonej z 9 zakładów na świecie. W ramach sieci polski oddział, który w swoim zespole posiada wysoko wykwalifikowanych koordynatorów i ekspertów procesu, odpowiada za standaryzację i unifikację procedur wytwarzanych serwohamulców i pomp hamulcowych we wszystkich zakładach. Polscy inżynierowie wykonują też mrówczą pracę, bez której na rynek nie mógłby wejść żadne nowe auto w Unii Europejskiej.
Każdy kierowca ma ten element w swoim aucie. Powstał w głowie polskiego inżyniera
Od 2012 roku przy zakładzie w Mirkowie działa Centrum Badawczo-Rozwojowe, które zatrudnia dziś ponad 90 inżynierów, wysoko wykwalifikowanych koordynatorów i ekspertów procesu. Zespół rozwija produkty z portfolio motoryzacyjnego Grupy Boscha, szczególnie w zakresie kolejnych generacji układów hamulcowych (np. Zintegrowanego Zespołu Mocy - z angielskiego Integrated Power Brake), a także odpowiada za standaryzację i unifikację procedur wytwarzanych serwohamulców i pomp hamulcowych we wszystkich 8 zakładach Bosch. Eksperci z Mirkowa są też odpowiedzialni za konstrukcję pierwszej generacji iBoostera i mechaniczne komponenty iBoostera 2 - czyli nowoczesnych, elektrycznych układów wspomagania hamowania (funkcje wspomagania realizuje silnika elektryczny bez jakichkolwiek elementów pneumatyki).
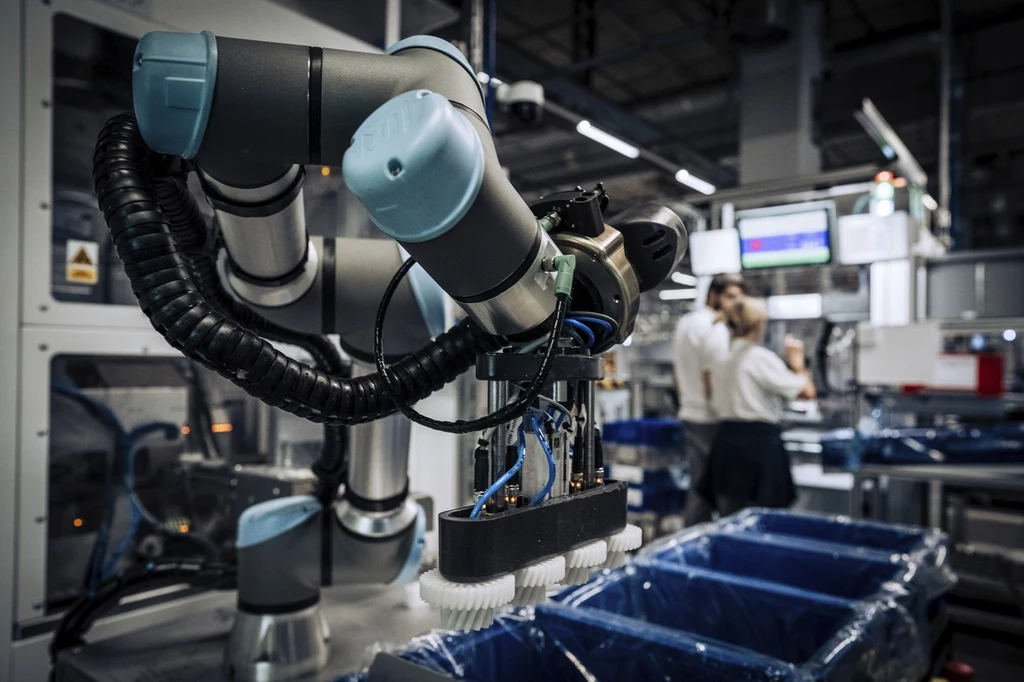
Codzienna mrówcza praca inżynierów spod Wrocławia polega też na projektowaniu kolejnych odmian zbiorniczków wyrównawczych płynu hamulcowego. Brzmi błaho, ale bez wsparcia inżynierów z Mirkowa na rynek nie trafiłby praktycznie żaden nowych samochód. Dość powiedzieć, że w skali roku pod Wrocławiem powstaje przynajmniej 20 zaprojektowanych od podstaw zbiorniczków płynu hamulcowego dla najróżniejszych światowych gigantów - od Grupy Volkswagena czy Toyoty, przez Forda, PSA (Stellantis) na Tesli kończąc. Praktycznie wszystkie budowane obecnie w Europie samochody tych koncernów mają pod maską zaprojektowane w Mirkowie zbiorniki płynu hamulcowego, a w zdecydowanej większości pracują w nich też inne komponenty (zespoły pompy hamulcowej, czujniki prędkości obrotowych kół) wyprodukowane na Dolnym Śląsku.
Jak wyciszyć pompę hamulcową? Dziwne problemy nowoczesnej motoryzacji
Fabryka pod Wrocławiem pochwalić się też może szeregiem laboratoriów badawczych i nietypowymi stanowiskami testowymi. W Mirkowie przeprowadzane są m.in. badania wytrzymałościowe oraz... wibroakustyczne. W kontekście produkowanych w fabryce iBoosterów, czyli zespołów pompy hamulcowej z elektrycznym serwem, może się to wydawać dziwne, ale nowoczesna motoryzacja staje przed szeregiem wyzwań nieznanych użytkownikom starszych pojazdów.
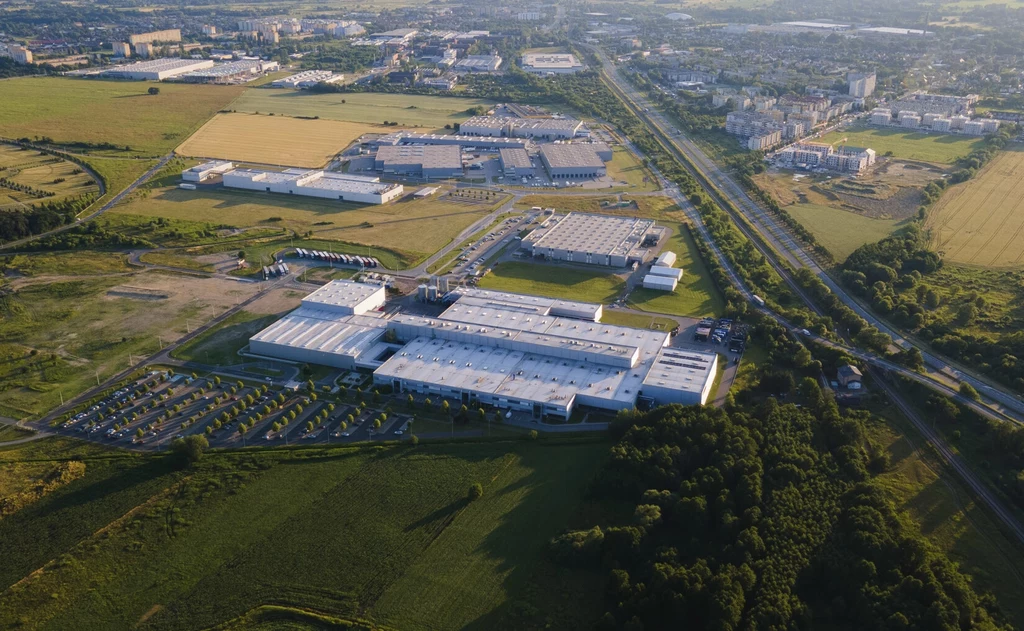
Pamiętajmy np. że jeździe nowoczesnym autem elektrycznym nie towarzyszą odgłosy czy wibracje silnika spalinowego, które "tłumiły" prace takich elementów, jak chociażby silnik wycieraczek czy - właśnie - elektryczne serwo hamulcowe. Konstruktorzy stają więc przed nowymi wyzwaniami dotyczącymi właśnie akustycznej charakterystyki ich pracy.
Inteligentny magazyn w fabryce Bosch pod Wrocławiem. Tak wgląda fabryka przyszłości
W oparciu o koncepcję Fabryki Przyszłości (Factory of the Future) i rozwiązań Przemysłu 4.0, w ramach rozbudowy podwrocławskiego zakładu, w fabryce Boscha w Mirkowie uruchomiono właśnie w pełni zautomatyzowany magazyn wysokiego składowania SILO. To ultranowoczesne rozwiązania, do którego obsługi nie są potrzebni żadni pracownicy. Rola człowieka ogranicza się tu wyłącznie do operowania wózkami widłowymi, których zadaniem jest dostarczenie na "taśmę" konkretnej palety. Dalej - za zamkniętymi drzwiami - wszystko dzieje się automatycznie. System sam decyduje, w które miejsce powinna trafić konkretna paleta i steruje automatycznymi dźwigami, które - jeżdżąc po specjalnych szynach - same odstawiają zapasy na magazynowe półki. Magazyn obsługiwany jest przez 6 automatycznych dźwigów, które rozkładają towar na regałach o wysokości nawet 17 metrów.
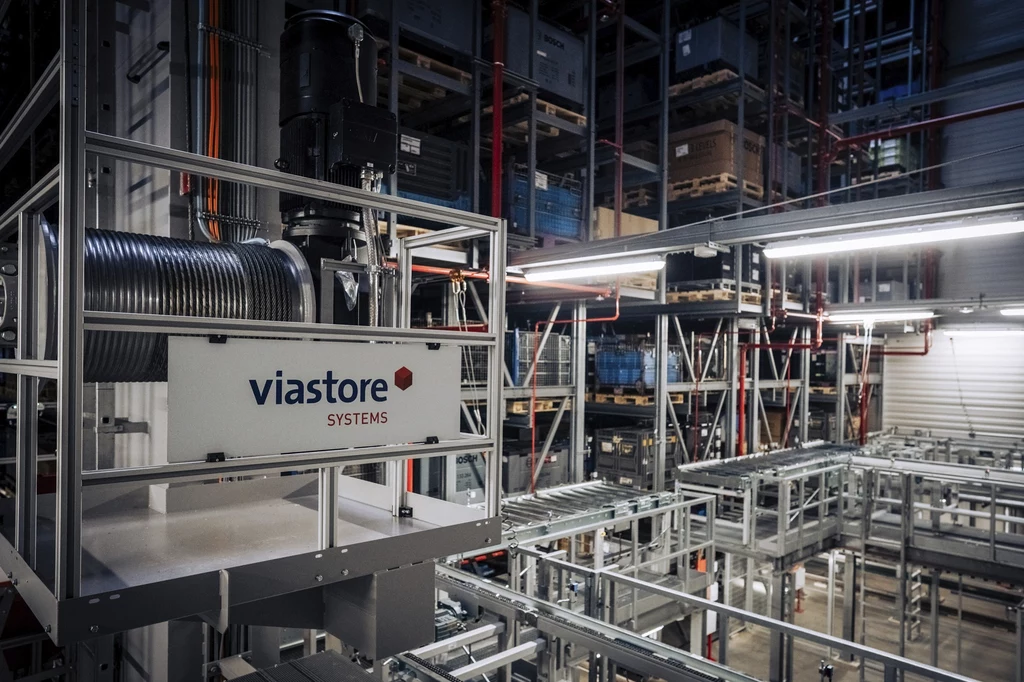
Co ciekawe, mowa o tzw. magazynie rozproszonym, gdzie - na tych samych regałach, znajdziemy zarówno komponenty niezbędne do bieżącej produkcji w zakładzie, jak i gotowe podzespoły czekające na wysłanie do klientów. Dziwne? To element polityki "bezpieczeństwa". W razie awarii jednego z dźwigów funkcjonowanie zakładu czy dostawy do klientów nie są zagrożone. Pełna integracja magazynu z systemem oprogramowania S/4HANA pozwala na planowanie zasobów poprzez wykorzystanie danych w chmurze w czasie rzeczywistym. Podwrocławska fabryka Bosch to pierwszy zakład produkcyjny Grupy Bosch, który wdrożył takie rozwiązanie.
Fabryka przyszłości to nie redukcja miejsc pracy
Przyglądając się nowoczesnemu magazynowi, którego same regały stanowią np. konstrukcję nośną budynku, można odnieść wrażenie, że postępująca automatyzacja to zagrożenie dla lokalnych miejsc pracy. Szefostwo wrocławskiej fabryki przekonuje, że to błędne myślenie. Wdrażana w Mirkowie koncepcja Fabryki Przyszłości i Przemysłu 4.0 nie zakłada zastępowania pracowników maszynami, lecz - szeroko rozumianą - optymalizację, na której zyskiwać mają właśnie pracownicy
Fabryka Przyszłości Bosch to wysoce produktywna organizacja, w której celem nadrzędnym jest eliminacja wszelki strat zasobów. Poza urządzeniami oraz infrastrukturą tworzą ją przede wszystkim ogromne ilości danych. Ich przetwarzanie opieramy o zaawansowane technologie cyfrowe, które efektywnie integrują procesy produkcyjne oraz logistyczne. Wszystkie nasze procesy i dane są konsekwentnie standaryzowane, a następnie digitalizowane. Nasza wizja rozwoju skupia się na osiągnięciu pozycji wiodącej firmy w dziedzinie rozwoju IoT (Internetu Rzeczy) oraz na byciu pionierem w dziedzinie zintegrowanego przemysłu - powiedział Piotr Pyzio członek zarządu Robert Bosch sp. z o.o. i dyrektor fabryki układów hamulcowych Bosch w Polsce.
Dzięki sieci okalających fabrykę czujników można precyzyjnie prognozować wydajność produkcji i zapobiegać awariom. Przykładowo - pracujące w zakładzie obrabiarki wyposażone są w czujniki wibracji czy np. liczniki zużycia sprężonego powietrza. Analiza bieżących danych potrafi wiec wskazać na problem na długo przed tym, zanim awaria maszyny wykluczy ją z pracy czy odbije się na jakości produkowanych podzespołów. Analiza odbywa się w tle na podstawie danych, bez ingerencji inżyniera procesu, a decyzje podejmowane są bezpośrednio przez model decyzyjny. Algorytm sugeruje rozwiązanie lub sam dostraja parametry procesu, działając w sposób prewencyjny, co bezpośrednio wpływa na optymalizacje procesów w fabryce.
Nowoczesność to również wspomaganie pracowników urządzeniami, które poprawiają bezpieczeństwo pracy i podnoszą jej wydajność. "Z powodzeniem stosujemy w codziennej pracy roboty współpracujące - coboty, które w sposób inteligentny i elastyczny automatyzują procesy. To rewolucja w zakresie zwiększenia wydajności oraz bezpieczeństwa. Ich zdolność do wykrywania obecności ludzi i reakcji na zmiany w otoczeniu pozwala na bezpieczną współpracę na tym samym obszarze roboczym
50 milionów części z Mirkowa. Pracują też w twoim aucie
Przedstawiciele Boscha podkreślają, że na liniach produkcyjnych podwrocławskiej fabryki wytworzono już ponad 50 milionów komponentów, które wpłynęły na poprawę bezpieczeństwa na drogach całego świata. Roczna produkcja zakładu to około 5 mln komponentów.
"Zmierzamy w kierunku urzeczywistnienia wizji pojazdu, który jest “smartfonem na kółkach". Wszystko to za sprawą oprogramowania odgrywającego coraz większą rolę w mobilności. To właśnie system obsługi i dostępne funkcje - obok samej mechaniki i prowadzenia pojazdu - wpływają na jakość doświadczeń w samochodzie. Dlatego dziś mówimy już o pojeździe opartym na oprogramowaniu, czyli SWdV (eng. Software defined vehicle)
Eksperci firmy prognozują, że rosnące znaczenie będzie mieć stopień integracji urządzeń i usług cyfrowych z samochodem. Funkcje łączności, automatyzacji i personalizacji będą w przyszłości coraz częściej wdrażane właśnie za pomocą oprogramowania. Tak samo stanie się w przypadku aktualizacji sprzętowych. Ta ewolucja nie tylko wpływa na rozwój i działanie, ale także umożliwia nowe modele biznesowe i rodzaje współpracy - tłumaczą.