Polski samochód elektryczny gotowy do produkcji. Powstał na Dolnym Śląsku
Przeszło 340 km z toną ładunku "na plecach". Taki wynik - w ramach testów Narodowego Centrum Badań i Rozwoju - uzyskał polski elektryczny samochód dostawczy EVAN1 z firmy Innovation AG. W jej siedzibie - w miejscowości Trójca u podnóża Gór Izerskich - gościliśmy niedawno z naszą kamerą. Dla fanów polskiej motoryzacji mamy dobre informacje. Pojazd jest praktycznie gotowy do produkcji.
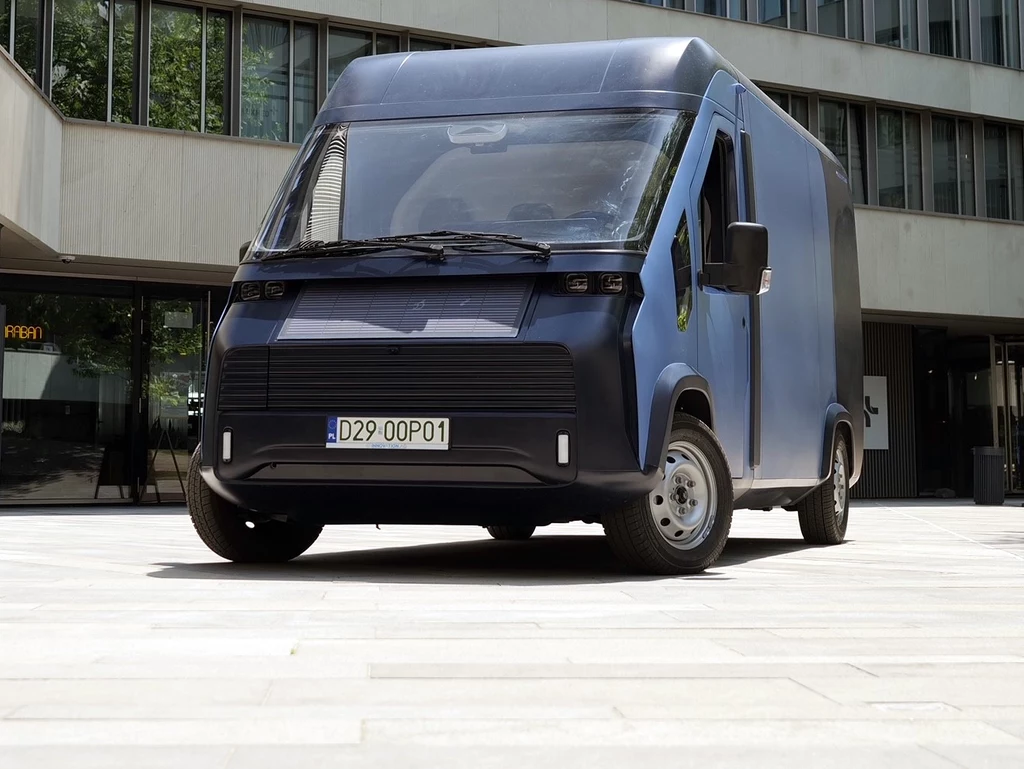
Spis treści:
Evan spod Zgorzelca to nie żadna makieta lecz prawdziwy, gotowy do produkcji pojazd, który bez kompleksów stawać może w szranki z elektrycznymi dostawczakami renomowanych marek.
Prototypy, jakie zobaczyć możecie na naszym filmie, powstały w ramach konkursu zorganizowanego przez Narodowe Centrum Badań i Rozwoju. Śmiało można jednak powiedzieć, że NCBiR nie był wcale głównym motorem ich powstania. Innovation AG, firma założona przez związanego ze światem sportów motorowych Alberta Gryszczuka (stąd litery AG w nazwie), od lat nosiła się z ambitnym zadaniem - stworzenia pierwszej w Polsce platformy dla elektrycznych samochodów dostawczych.
Innovation AG - polscy eksperci od elektryków
Porywanie się z motyką na słońce? Niekoniecznie. Przypominamy, że w Innovation AG powstał m.in. elektryczny Sokół 4x4, a firma dokonała wielu udanych "ekokonwersji" - czyli przeróbek różnej maści pojazdów (głównie dostawczych) na elektryczne. W Trójcy pod Zgorzelem powstało też wiele aut sportowych, m.in. takie, którymi na trasach morderczych rajdów przełajowych ścigał się Adam Małysz.
Dane pozyskane na przy okazji konwersji i serwisowania przerobionych na elektryki pojazdów pozwoliły ekipie Innovation AG na opracowanie autorskiego systemu zarządzania energią o nazwie EVACT. Staraniem polskich innowatorów powstało serce zarządzania pojazdem - jego napędem, komunikacją z podzespołami, sterowaniem przepływem energii czy też oddawania jej poza pojazd (system V2G - vehicle to grid).
EAGLE czyli polska platforma dla dostawczych samochodów elektrycznych
Dysponując zaawansowanym systemem zarządzania pojazdem naturalnym krokiem wydawała się budowa własnego samochodu elektrycznego.
Firma - zgodnie z nazwą - podeszła do tematu w innowacyjny sposób. Zamiast skupiać się na projekcie konkretnego auta, postawiono sobie dużo ambitniejsze zadanie - stworzenie od podstaw skalowalnej platformy, która mogłaby stanowić bazę dla najróżniejszych wersji pojazdu. Co więcej - od początku zakładano, że same pojazdy muszą być możliwe do zbudowania w warunkach manufaktury.
Prace nad platformą w całości prowadzone były w Polsce. W ich efekcie powstała platforma o nazwie EAGLE (Orzeł), na którą składają się:
- podwozie,
- układ hamulcowy,
- układ napędowy,
- układ kierowniczy,
- zawieszenie.
Wszystkie kluczowe elementy platformy, jak również cały projekt techniczny, są autorstwem polskich inżynierów i mechaników. Nie jest to więc zbiór przypadkowych części, jakie kupić można w hurtowniach motoryzacyjnych. Oprócz samej ramy, w Polsce - od podstaw - powstały też m.in. takie elementy, jak chociażby zwrotnice czy wahacze.
EVAN1 ze Zgorzelca - gotowy projekt czeka na inwestorów
Jeżdżące prototypy nie są więc szczytem możliwości firmy spod Zgorzelca, a jedynie skromnymi demonstratorami jej możliwości. Oba mają baterie o pojemności 105 kWh i elektryczne silniki trakcyjne o mocy 160 kW. Same baterie wykonane zostały wprawdzie przez chińskiego kooperanta, ale ich projekt powstał w Zgorzelcu. Napęd przekazywany jest na koła przedniej osi, ale sama platforma pozwala też na budowanie aut 4x4.
Nietypowe, jak na dzisiejsze standardy, są też plany biznesowe polskiej firmy. W rozmowie z Interią prezes Innovation AG - Albert Gryszczuk - zdradza, że niewielkie przedsiębiorstwo nie ma ambicji samodzielnej produkcji EVANa.
Zamiast tego skupia się raczej na dostarczeniu potencjalnym inwestorom całościowego rozwiązania w postaci gotowej do produkcji platformy. Same EVANy stworzone w ramach konkursu NCBiR mają już dopuszczenie drogowe i przechodzą właśnie wszelkie niezbędne badania homologacyjne. Mówiąc wprost - zamiast uruchamiać produkcję Innovation AG planuje raczej sprzedawać licencję na wykorzystanie stworzonej samodzielnie platformy.
To ciekawy pomysł, jeśli wziąć pod uwagę, że - od samego początku - projektowano ją w taki sposób, by auta można było budować w warunkach manufaktury. Przykład - najdłuższy z elementów ramy pojazdu ma zaledwie 2,5 m długości - do jego wykonania nie trzeba więc dysponować żadnym specjalistycznym sprzętem. Możliwość budowania auta w warunkach manufaktury i szybkiego dostosowywania pojazdu do nietypowych wymogów użytkowników to jeden z największych atutów polskiego projektu.
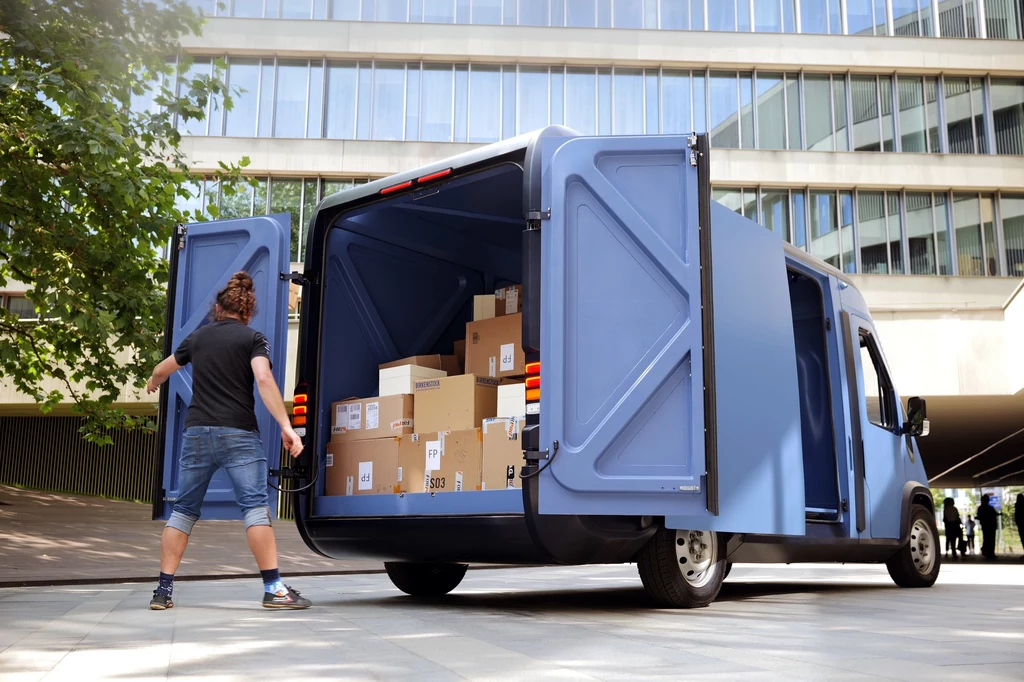
W dobie wielkiej transformacji motoryzacji, niewielkie firmy, jak właśnie Innovation AG, są w stanie dużo elastyczniej dopasowywać się do wymogów nabywców niż wielkie koncerny, które kierują swoje produkty do klientów masowych. Mając bezpośrednie wsparcie zespołu projektowego, konkretny klient może przecież zażyczyć sobie dostosowania pojazdu do nietypowej zabudowy lub warunków eksploatacji.
Mowa tu chociażby o kopalniach czy firmach kurierskich dysponujących własnymi flotami. W takich przypadkach zamówienia nie muszą iść w tysiące sztuk, a możliwość samodzielnej budowy i - co równie ważne - późniejszego serwisowania pojazdu może być ogromnym atutem.
EVAN z Innovation AG w szczegółach
EVAN z Innovation AG w szczegółach
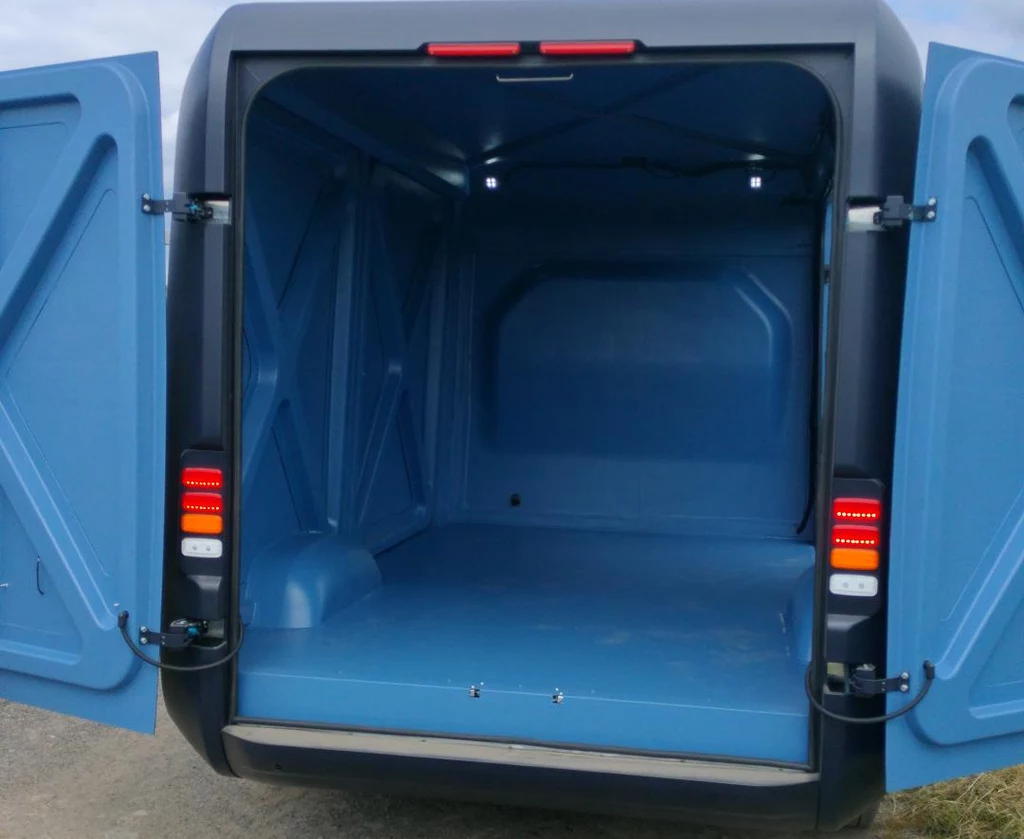
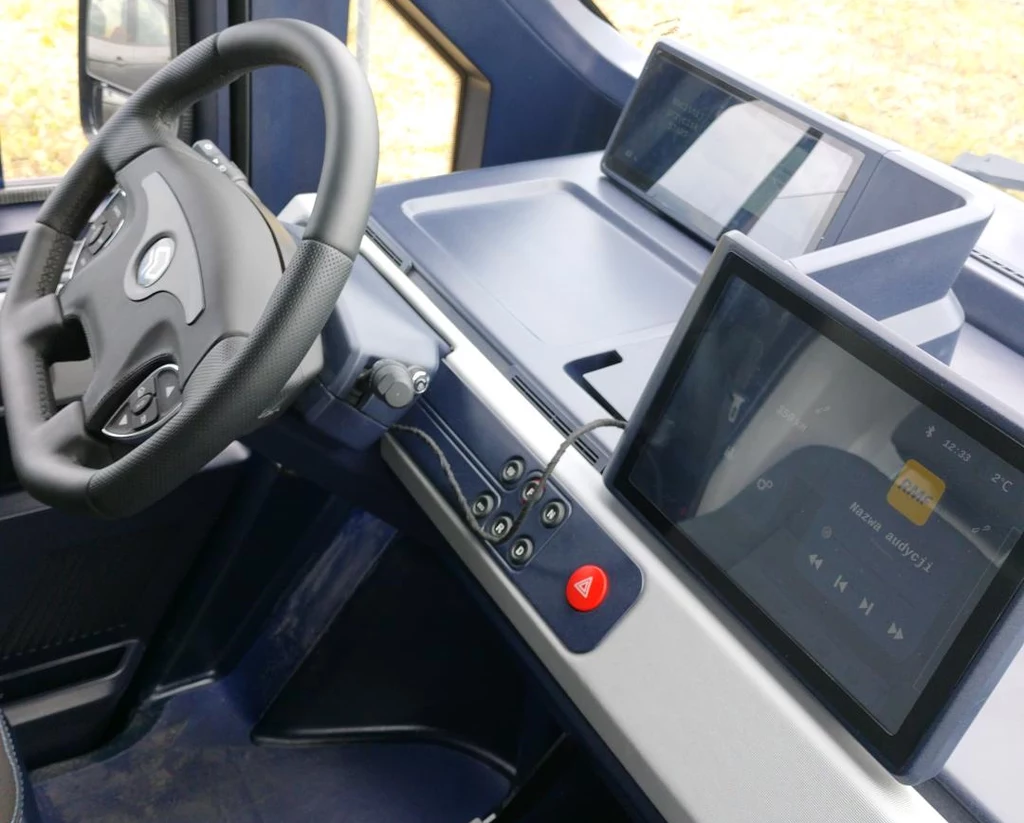
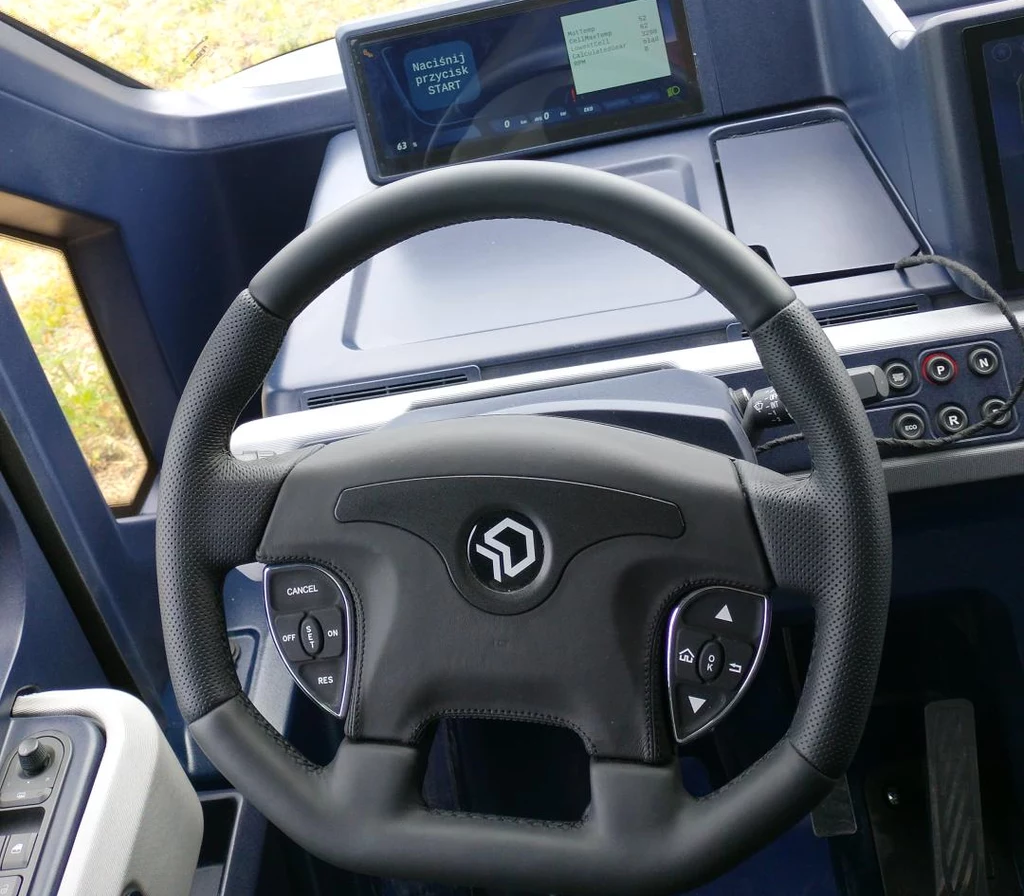
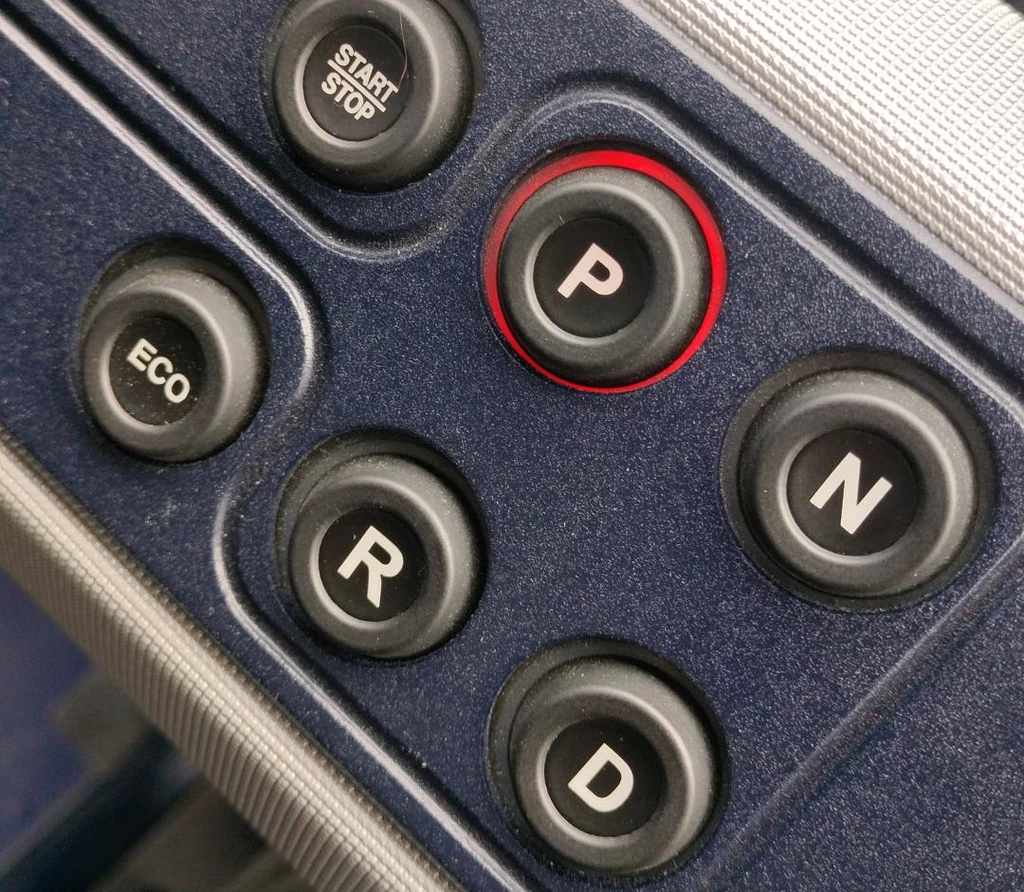
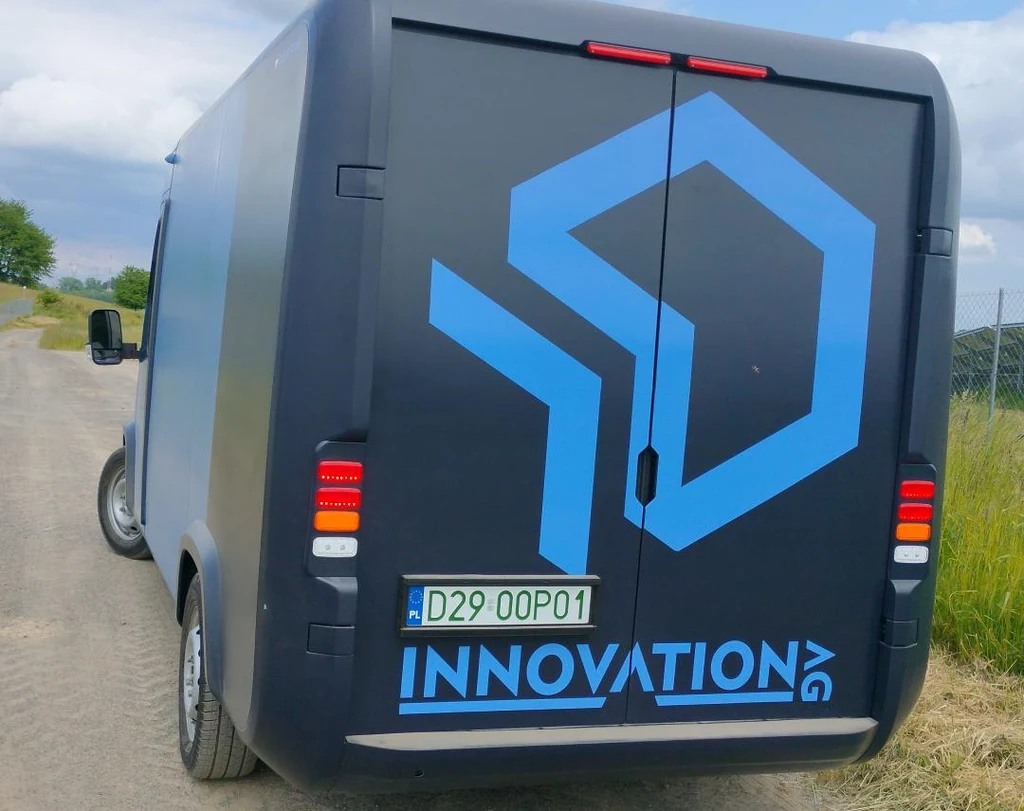
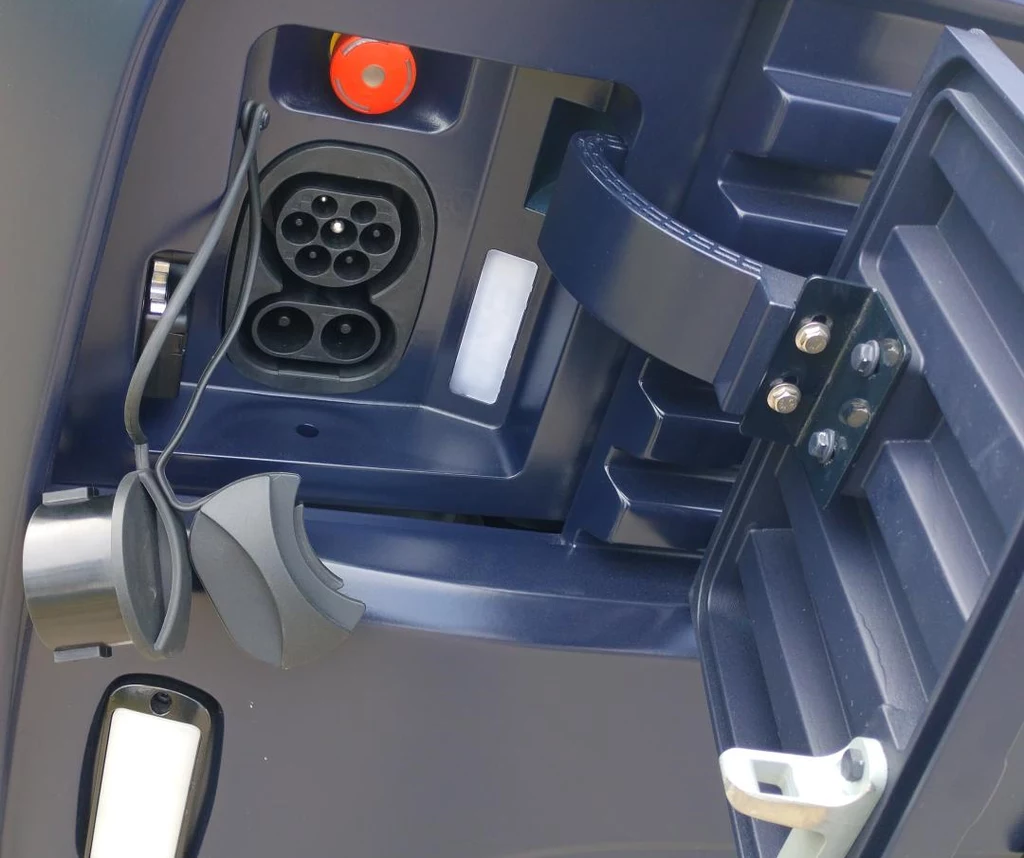
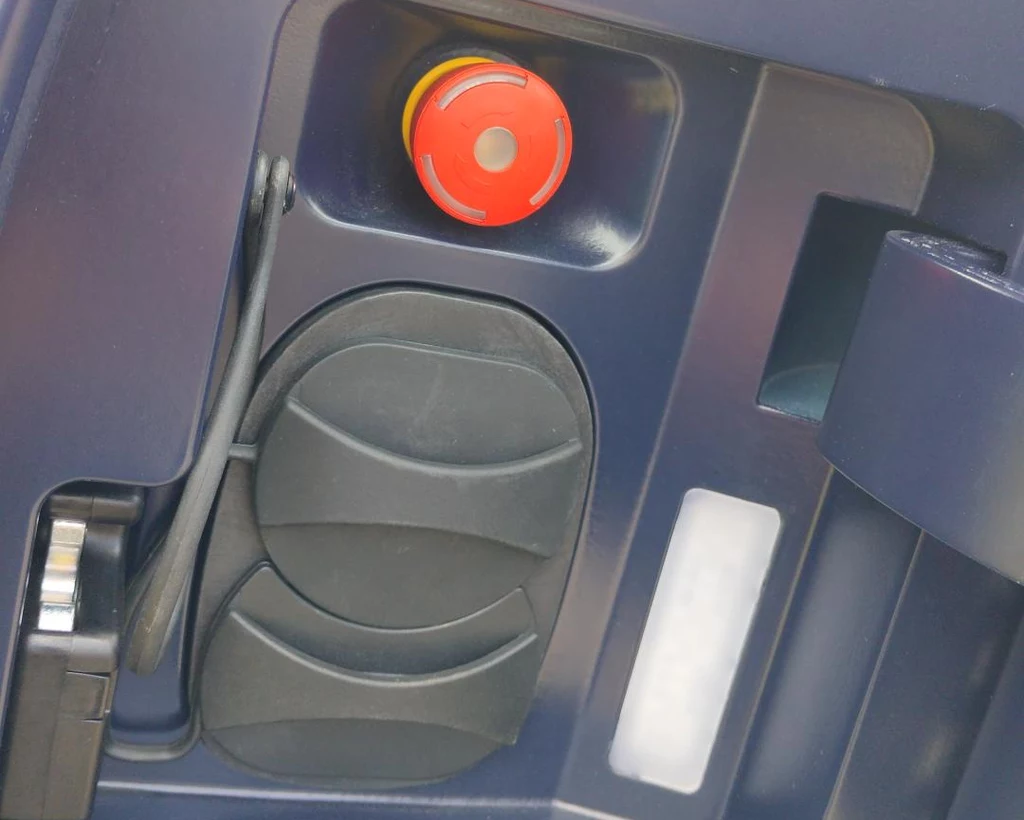
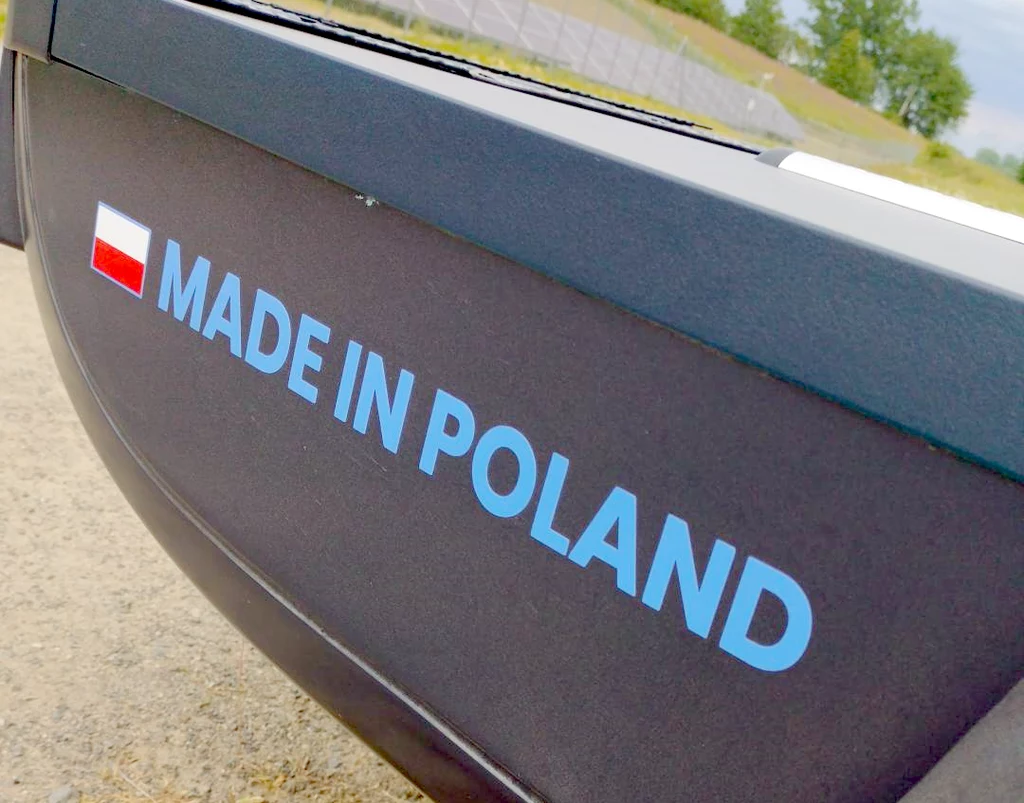
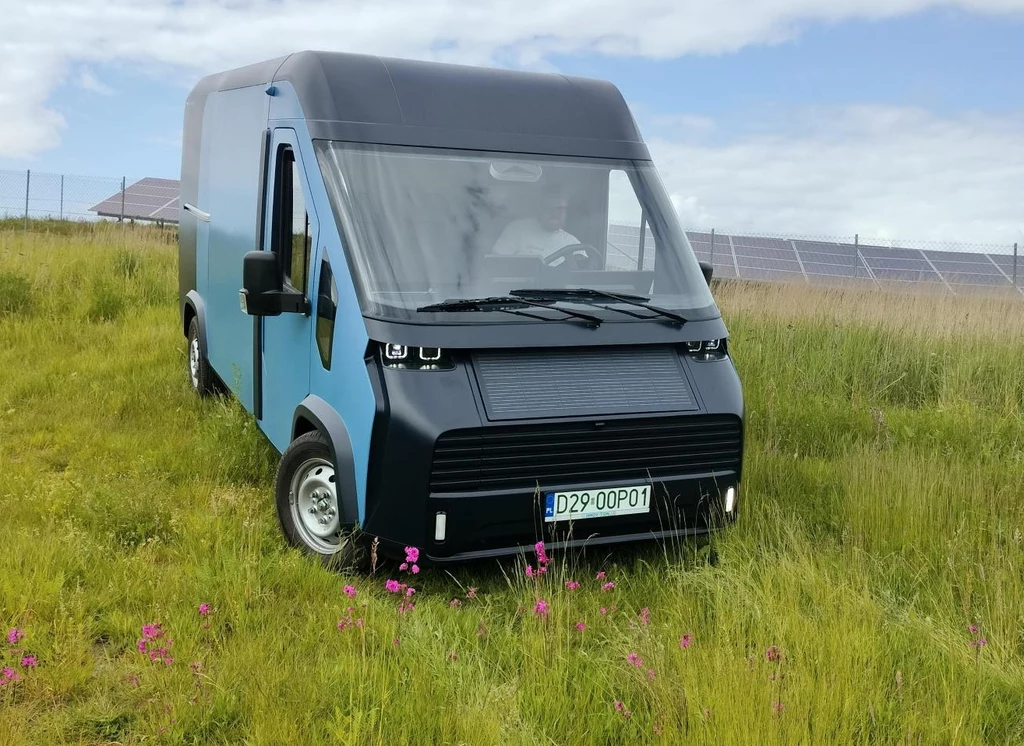
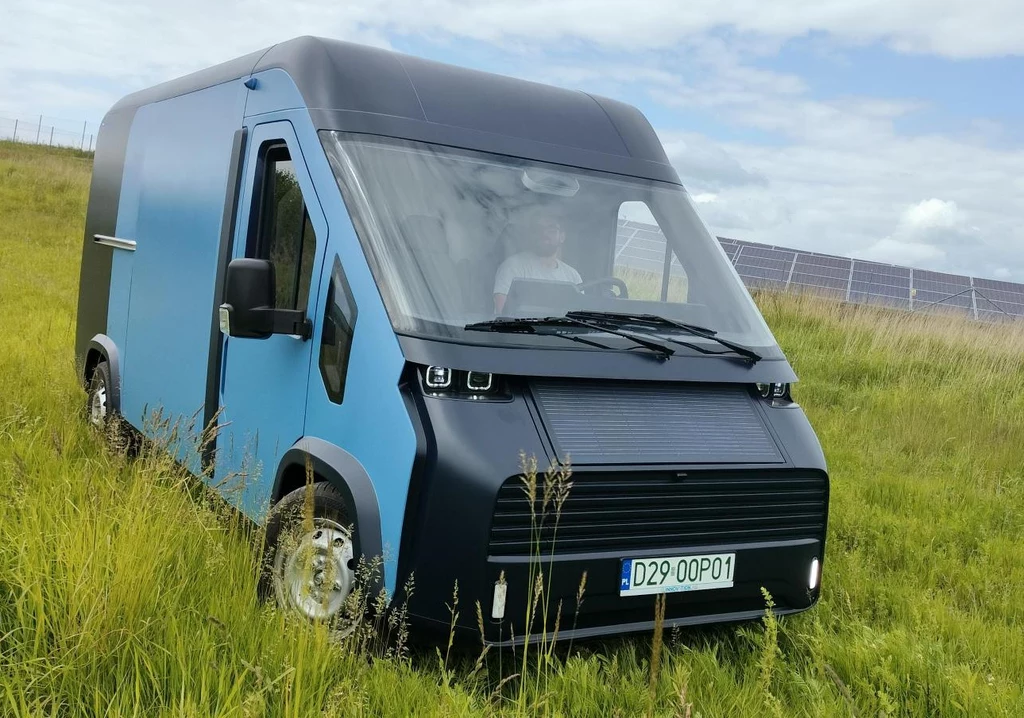
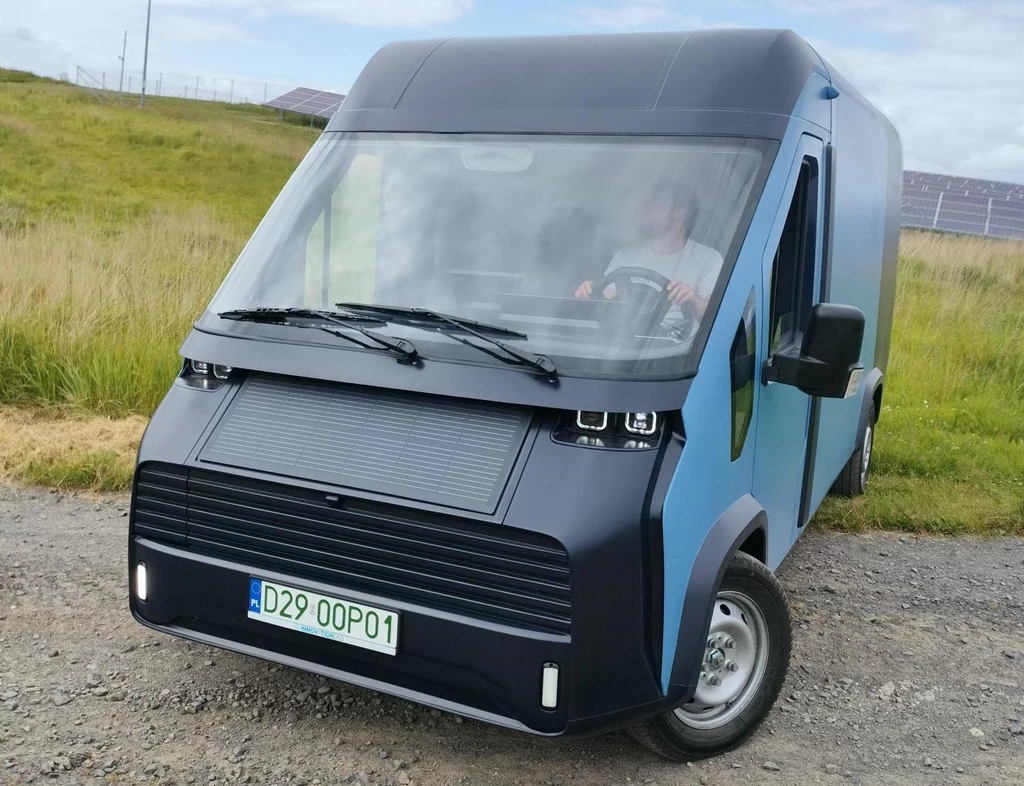