Wizyta w Renault ElectriCity – widzieliśmy, jak powstaje Megane E-Tech
Korzystając ze specjalnego zaproszenia firmy Renault, udaliśmy się do jednej z najstarszych fabryk producenta, umiejscowionej na przedmieściach francuskiego miasta Douai. W gąszczu hal i magazynów mogliśmy podziwiać, jak powstaje nowy bezemisyjny model Megane E-Tech. Byliśmy także świadkami montowania samochodowych baterii elektrycznych.
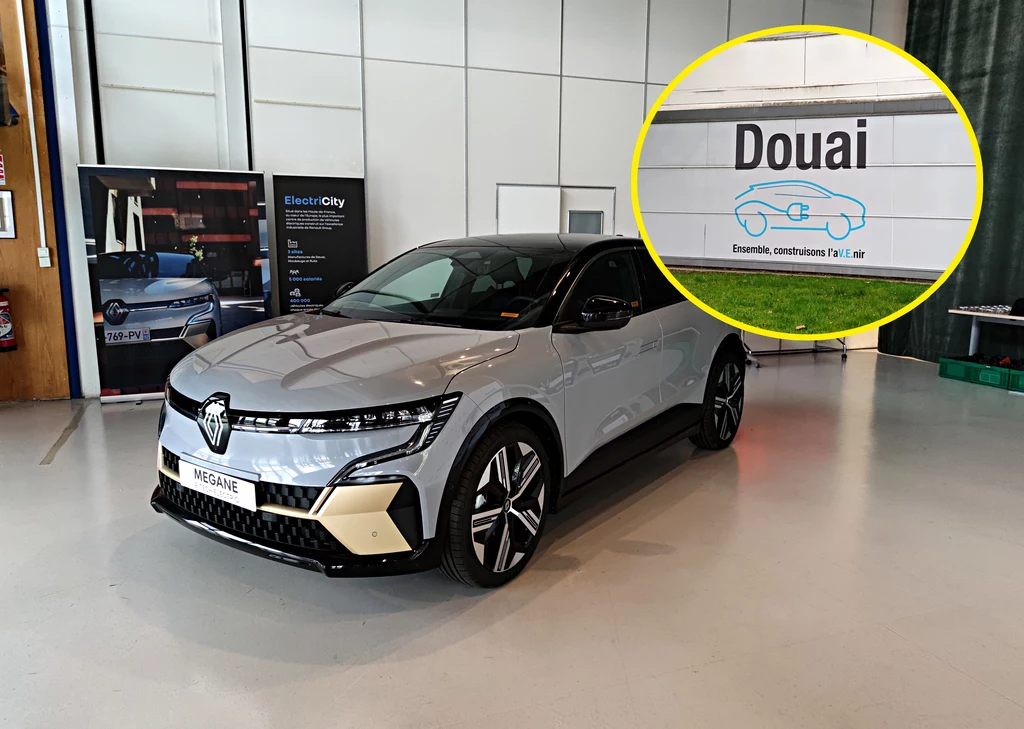
Renault Megane E-Tech to prawdziwa rewolucja w gamie modelowej francuskiego producenta. Chociaż elektryczny crossover w niczym nie przypomina swojego kultowego przodka, już teraz wzbudza zainteresowanie swoją niebanalną stylistyką, nowoczesnymi technologiami oraz zaskakującą przestronnością. Gdy zatem do naszej redakcji dotarło zaproszenie na zwiedzanie fabryki w której powstaje, nie mogliśmy odmówić.
Renault ElectriCity
Wspomniana fabryka mieści się na przedmieściach francuskiego miasta Douai. Sam zakład, w którym obecnie powstaje Megane E-Tech, to jedynie część gigantycznego ośrodka rozwojowego samochodów elektrycznych, noszącego dumną nazwę ElectriCity. W jego skład wchodzą jeszcze dwa inne obiekty zlokalizowane w północnym regionie administracyjnym Hauts-de-France. Wśród nich jest fabryka w Maubeuge, która odpowiada za produkcję m.in. nowego Renault Kangoo oraz zakład w Ruitz, stawiający nacisk na wytwarzanie komponentów elektrycznych.
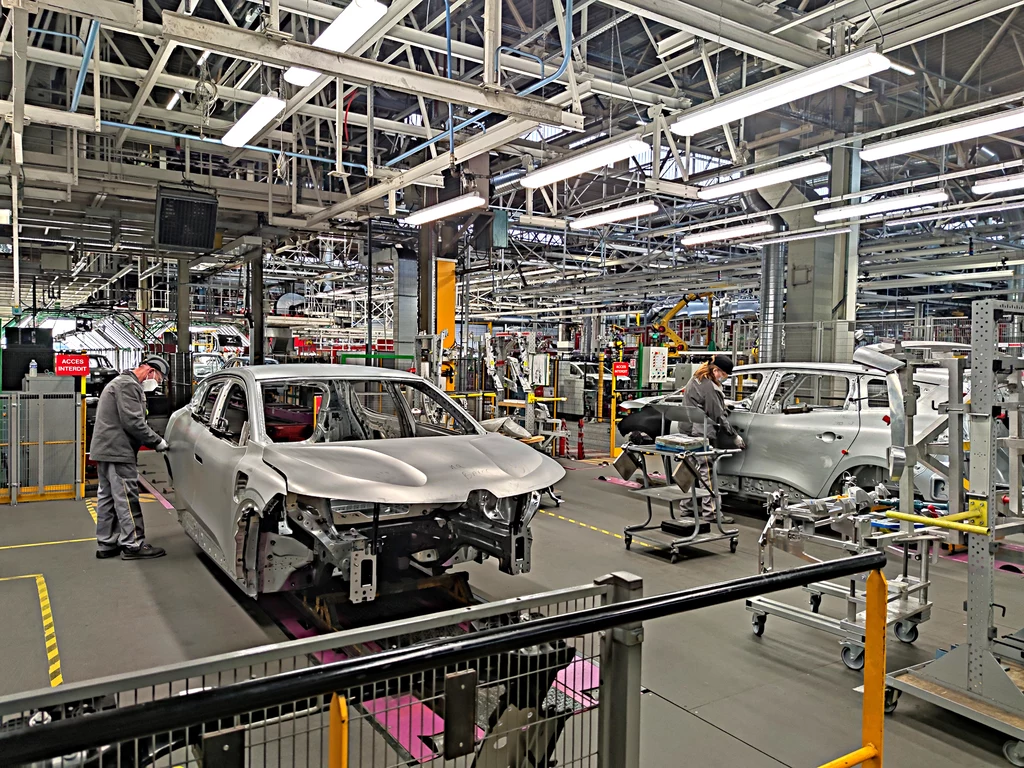
Zanim jednak będzie nam dane zagłębić się w liczne, wielopiętrowe hale produkcyjne, wizytę rozpoczynamy od krótkiego wstępu, przybliżającego historię fabryki. W trakcie opowieści dowiadujemy się m.in. o tym, że zakład w Douai powstał w 1970 roku i podczas ponad 50-letniej historii z jego taśm zjechało w sumie 10 milionów pojazdów. Wśród nich warto wymienić takie modele, jak Renault 11, Renault 19, czy kultowy już Renault 5. Punktem zwrotnym dla całego zakładu był 2018 rok, kiedy to przydzielono go do pracy nad pojazdami opartymi na nowej modułowej platformie CMF-EV - dedykowanej do produkcji samochodów elektrycznych. Od tego czasu całość została przeprojektowana specjalnie pod kątem wytwarzania nowej generacji, bezemisyjnych pojazdów, których głównych reprezentantem jest wspomniany już Megane E-Tech. Oczywiście wśród linii montażowych wciąż można wypatrzeć modele spalinowe, takie jak Espace, Scenic, czy nawet ostatnie sztuki Talismana - bez wątpienia to jednak elektryczny Megane ma tu wyraźną przewagę liczebną.
Zwiedzanie fabryki Renault - linia montażowa i lakiernia
Zwiedzanie rozpoczęliśmy od wielkiej hali, w której znajduje się główna linia montażowa. To właśnie tam są dopasowywane oraz łączone w całość liczne elementy karoserii samochodu. Niemal całość prac wykonują specjalne roboty przemysłowe, które nie tylko samodzielnie podają poszczególne elementy, odpowiednio je dopasowują, ale także zespalają ze sobą przy pomocy różnych metod - najczęściej spawania oraz zgrzewania. Praca odbywa się na nawet kilku poziomach, podzielonych piętrami. Pomiędzy nimi konstrukcje przemieszczają się na gigantycznych szynach lub są transportowane windami.
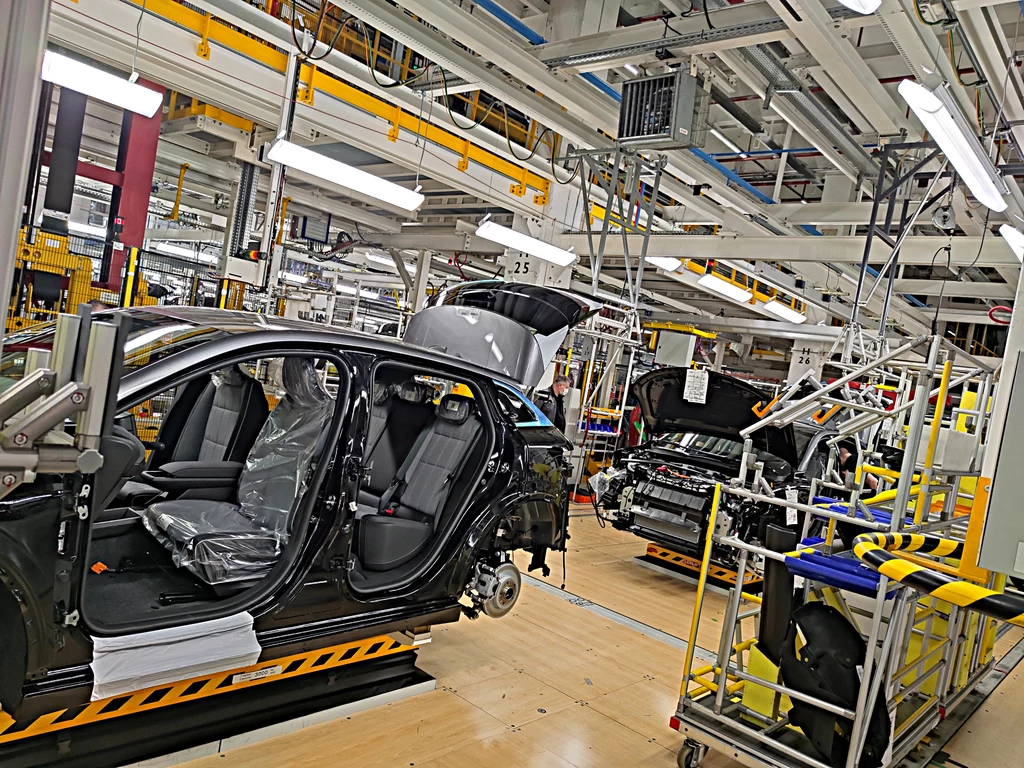
Przyznać trzeba, że poziom zautomatyzowania całości robi ogromne wrażenie. Idealnie zsynchronizowane roboty przy akompaniamencie wystrzeliwanych w górę iskier, potrafią wprowadzić człowieka w trudny do zracjonalizowania, przyjemny trans.
Gdy poszczególne elementy karoserii są już ze sobą połączone, przychodzi pora na kontrolę jakości ich spasowania. Następnie cała konstrukcja rusza do lakierni. Proces malowania blach także jest w pełni zautomatyzowany. Z uwagi na niebezpieczeństwo związane z unoszonymi w pomieszczeniu pyłami, dostęp do pomieszczeń lakierniczych był jednak niedostępny.
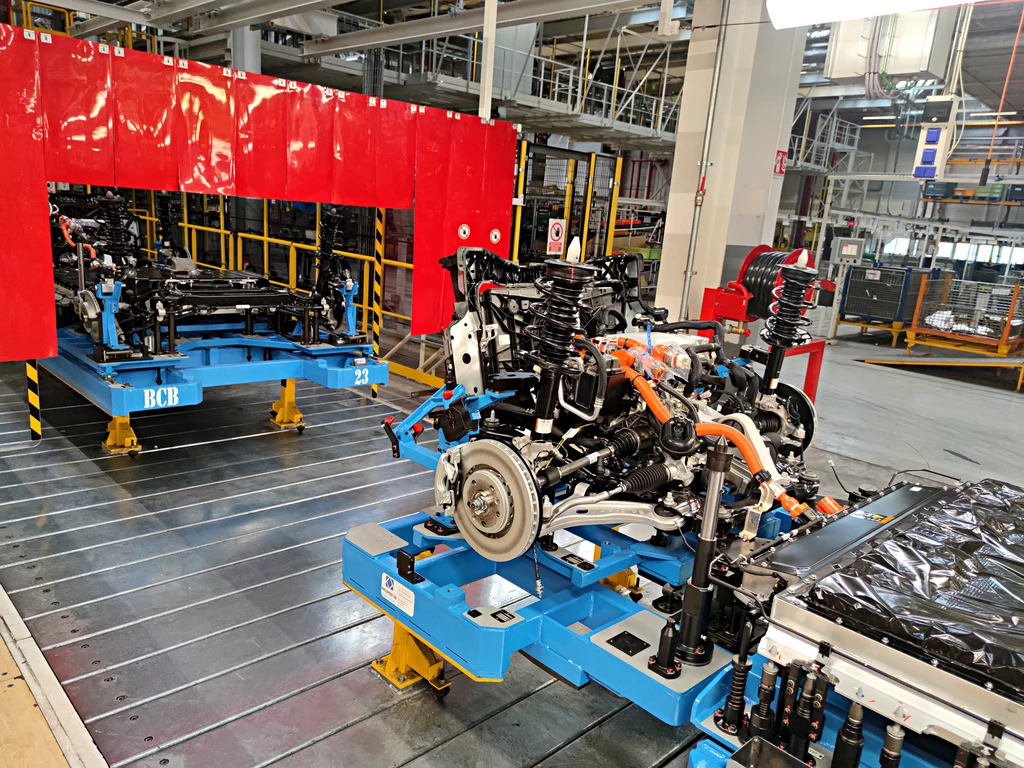
Zwiedzanie fabryki Renault - linia produkcyjna i kontrola jakości
Polakierowane karoserie są następnie transportowane do gigantycznej, jednopoziomowej hali w której znajduje się główna linia produkcyjna. Ta ma ponad kilometr długości, a wzdłuż niej mieści się 400 stanowisk roboczych, gdzie odbywa się montaż silników, podwozia i elementów wyposażenia wnętrza. To właśnie tam pracownicy przy ciągłej współpracy z odpowiednio zaprogramowanymi robotami, montują kolejne elementy samochodu i sprawdzają ich jakość. Wszystko działa jak dobrze zestrojona maszyna, a dzięki czytelnie opisanym procesom, każdy z pracowników dokładnie wie, co ma robić.
Jednym z najważniejszych etapów jest chwila łączenia nadwozia z podwoziem. Później następuje jeszcze zabudowa frontu, montaż siedzeń oraz rzecz jasna kół. Cięższe elementy, takie jak drzwi, czy klapa bagażnika są montowane przy współpracy z maszynami. Drobniejsze i lżejsze części są segregowane, a następnie dostarczane przy pomocy samodzielnie poruszających się robotów transportowych wprost do stanowiska danego pracownika. Renault chwali się także wysoką ergonomią pracy, dzięki automatycznie dostosowującej się wysokości montowanego samochodu do wykonywanej czynności. Na końcu auto zjeżdża z linii na własnych kołach poprzez tunel świetlny i trafia na testy.
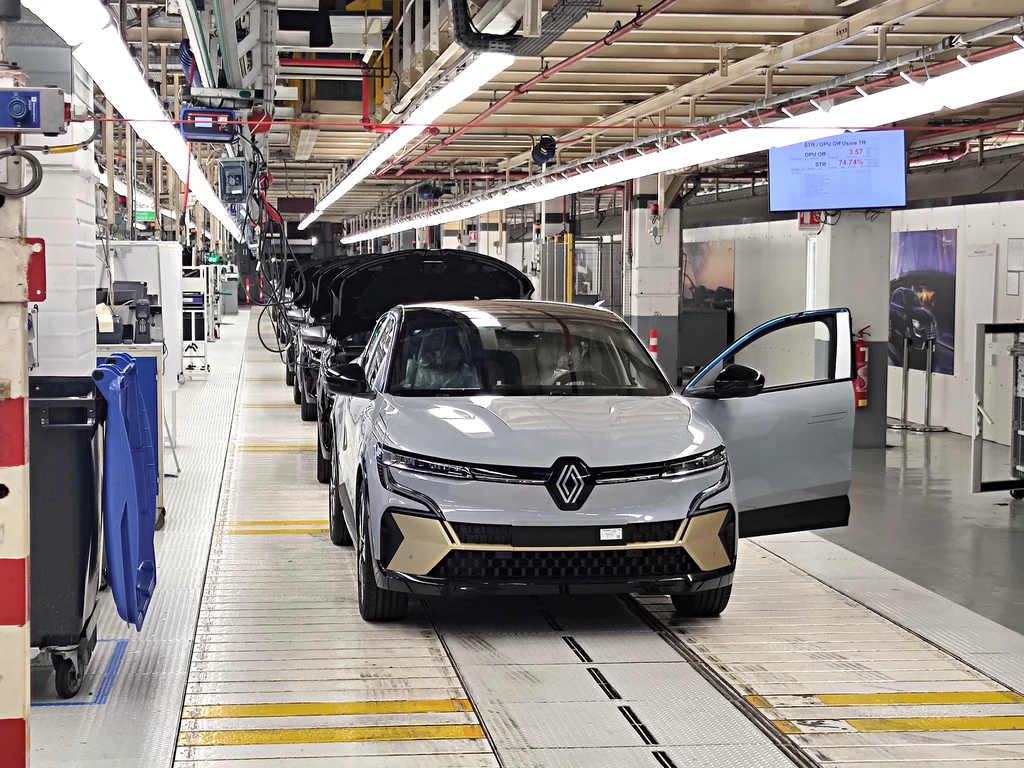
Te także odbywają się we wspomnianym budynku. Kontrolerzy sprawdzają spasowanie elementów zawieszenia, układu kierowniczego, działanie elektroniki oraz m.in. pojemność baterii.
Zwiedzanie fabryki Renault - ogniwa z polskiej fabryki
Będąc przy bateriach nie sposób nie wspomnieć o ostatnim pomieszczeniu, które dane nam było zobaczyć. Mowa o umiejscowionym na najwyższym piętrze warsztacie, w którym odbywa się ich produkcja.
W zasadzie chodzi o montaż poszczególnych modułów, począwszy od umiejscowienia samych ogniw, aż po podpięcie okablowania. Gotowe konstrukcje przechodzą następnie przez testy bezpieczeństwa. Istotnym elementem francuskiej konstrukcji jest m.in. żółty korek znajdujący się na module baterii. Jak poinformował nas przedstawiciel Renault - wskazuje on miejsce umożliwiające łatwe zalanie, a tym samym zgaszenie palących się ogniw. System jest podpięty do komputera pokładowego, który w razie wykrycia zderzenia oraz wypadku, automatycznie wyświetla instrukcje sprawnego zapobiegnięcia pożarowi.
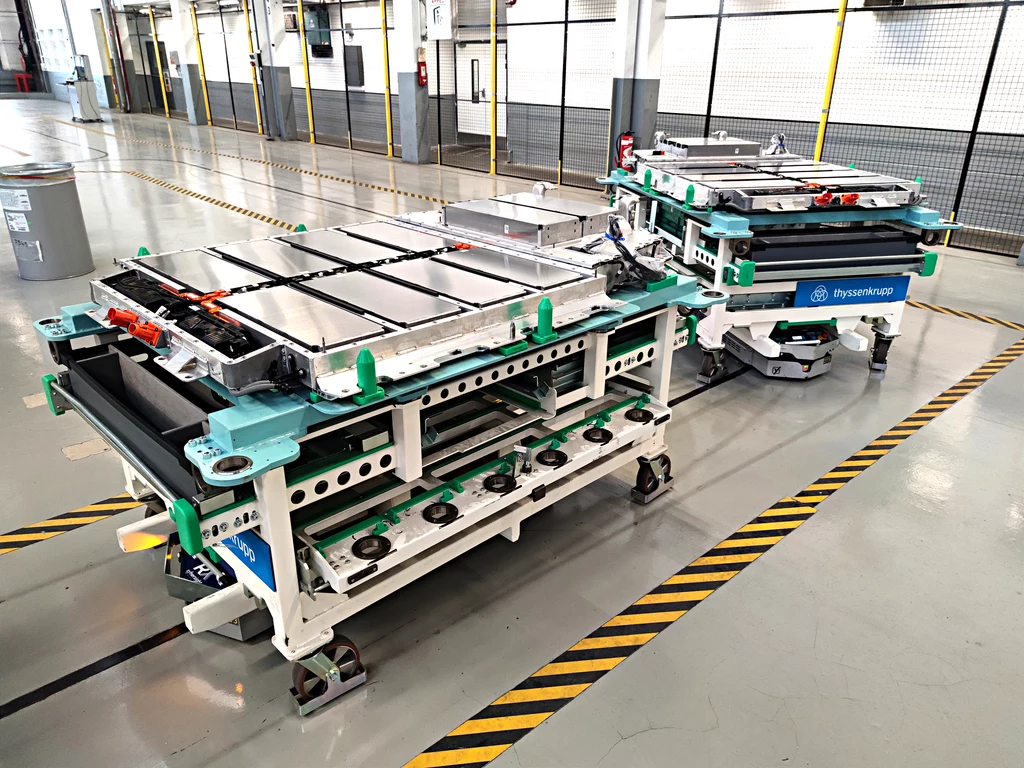
Całe pomieszczenie jest stosunkowo nowym obiektem w fabryce. Co ciekawe - stanowi zaledwie przedsmak przed planami wybudowania potężnej "megafabryki" baterii elektrycznych. Do tego czasu ogniwa, które wykorzystuje Renault pochodzą z polskiej fabryki LG pod Wrocławiem.